How Clean does Clean have to be for Recycle Water Quality?
When contemplating wastewater recycling to be used for process waters there are many filtration technologies to consider. Common filtration technologies include microfiltration (MF), ultrafiltration (UF), nanofiltration (NF) and reverse osmosis (RO). But how do you decide what level of filtration is necessary for your operations?
One of the factors businesses must take into consideration is determining How Clean does Clean have to be in order to reuse the wastewater back into the process flow?
Does the recycle water have to meet potable water quality parameters? Frequently recycle water programs are put in place due to the high costs of potable water. So, does recycle water need to meet that level of quality?
The primary difference between microfiltration, ultrafiltration and nanofiltration is the pore size of the membrane. With each different filtration process a variety of elements get either blocked or pass through with the water. Below is a diagram to demonstrate this.
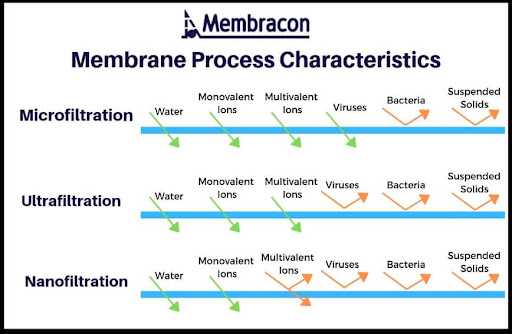
Microfiltration (MF) and ultrafiltration (UF) are both filtration processes where the wastewater is passed through a membrane that removes particulates that are too large to fit through the pores, resulting in a purified liquid. The particulates remain in the recirculation flow and is slowly bled from the system as a concentrate discharge.
The degree of purification depends on the contaminants in the liquid and the pore size of the membrane. These levels of filtration are commonly used in prefiltration to meet effluent discharge limitations or for further separation of process streams that need a tighter level of filtration such as nanofiltration or reverse osmosis.
Microfiltration and ultrafiltration are more similar to each other than different. MF and UF are both separation technology processes that use membranes to remove the contaminants in the process fluid. Membrane filtration can remove various particulates, bacteria, organic material, and certain dyes, improving odor, taste, color, etc., and are used for various process separation, purification, and concentration processes.
Microfiltration is used to separate suspended solids or colloidal particles between 0.1 and 10 μm in diameter from the wastewater.
Ultrafiltration membranes have pore sizes in the range of 0.02 – 0.05 microns, which contributes to the production of high-quality water; the pore-size range means that the purification process is characterized by a high removal capability of bacteria, viruses, colloids, and silt.
Nanofiltration has a pore size range of 0.001-0.01um. NF membranes can filter particles up to and including some salts, synthetic dyes, and sugars, however, it is unable to remove most aqueous salts and metallic ions.
Filtration Process
The wastewater passes through the membrane layer inside a multichannel filter element at a high velocity. Driven by pressure, the filtrate passes through the membrane layer vertically while the solids and large molecules continue to recirculate in the feed water. These solids and large molecules will be periodically discharged through the concentrate stream to effluent or to a concentrate holding tank for post treatment.
Ceramic filter membranes have many unique advantages compared to polymeric membranes:
- Excellent Resistance to Acid, Alkaline and Oxidizing Chemicals
- Solvent Stability
- High Thermal Stability
- Fine Separability with Narrow Pore Size Distribution
- Excellent Mechanical and Abrasive Resistance
- Extremely Long Work Life
- Compact Multi-Channel Geometry and high Permeability are Optimized for Bulk Flow Applications
Membrane Modules
The stainless-steel module is filled with ceramic membrane filter elements. Based on different flow rate and applications the number of filter elements and modules can vary. The modular design allows protection of the ceramic filter elements. Vibration reduction locks the membranes in place to prevent breakage which can lead to membrane failure. The design of the modules allows for forward flow, back flow, and back pulse flow through the pores to keep the membranes clear during operation.
The stainless-steel modules allow for aggressive chemical cleaning at elevated temperatures for the ceramic filter elements. These cannot always be achieved in non-metallic modules.
Ceramic membranes get great separation results due to its high mechanical strength, large amount of penetration, easy cleaning and narrow bore diameter distribution while it can be used for a much longer time because of its resistance to high temperature, chemical corrosion and microorganisms.
How Clean Does It Have To Be?
Ceramic Microfiltration can be used for a number of wastewater recycling or product recovery applications.
Example #1 – Metalworking Fluids
Metal parts are removed from wax molds leaving particulates, oils and greases, and cleaners in the rinse waters. Client wants to reuse/recover as much of the rinse water as possible to minimize freshwater usage.
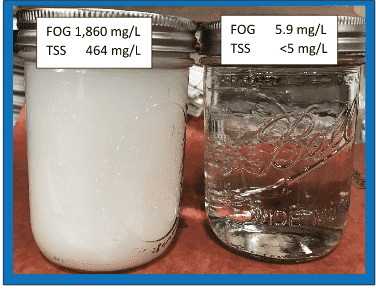
Many industrial dischargers have installed
dissolved air flotation (DAF) systems to
achieve compliance with local effluent
discharge limitations. In many plants, the
effluent wastewater clarity looks
extremely good. There is little to no TSS
carryover, possibly some foam due to
cleaners or detergents used upstream,
and oil and grease concentrations less
than 100 mg/L.
This effluent might be able to be used as
reuse water but there is a need to ensure
that the oil and grease concentrations are
lower and any TSS is almost non-existent.
Filtering the DAF effluent through a
ceramic microfiltration system may
produce the reuse water quality for the
industrial application.
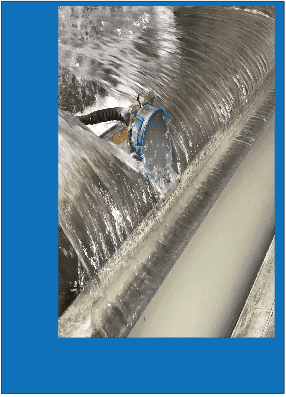
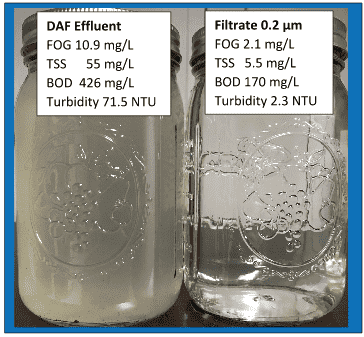
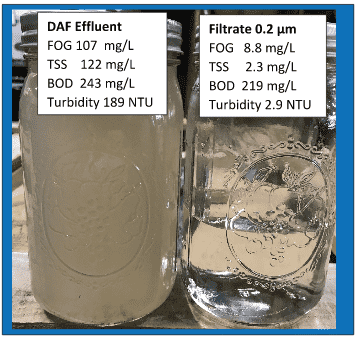
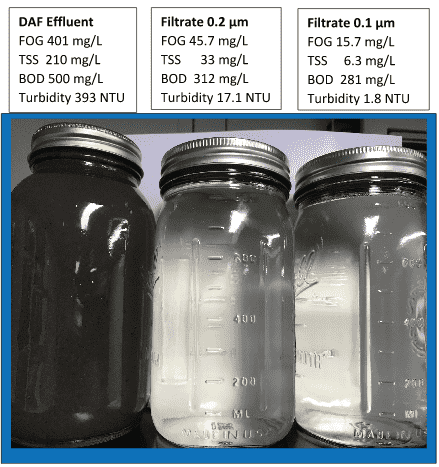
Membrane filtration systems generate a wastestream referred to as the concentrate. Depending upon the wastestream source the concentrate can become highly concentrated with Total Suspended Solids (TSS) and Fats, Oils, and Greases (FOG). These pollutants need to be disposed. The concentrate cannot be discharged to the effluent sewer because it will lead to noncompliance.
When using microfiltration or ultrafiltration for recycling DAF effluent, the majority of the FOG and TSS pollutants are removed from the wastewater. This lighter wastewater loading allows the filtration systems to process the wastewater longer without having to stop frequently for membrane cleaning.
In addition, the concentrate can be discharged back into the wastewater equalization tank for processing through the DAF to remove the TSS and FOG loadings. It is a win-win method to maximize recycle water applications.